How sterility Isolators are used in the pharmaceutical industry
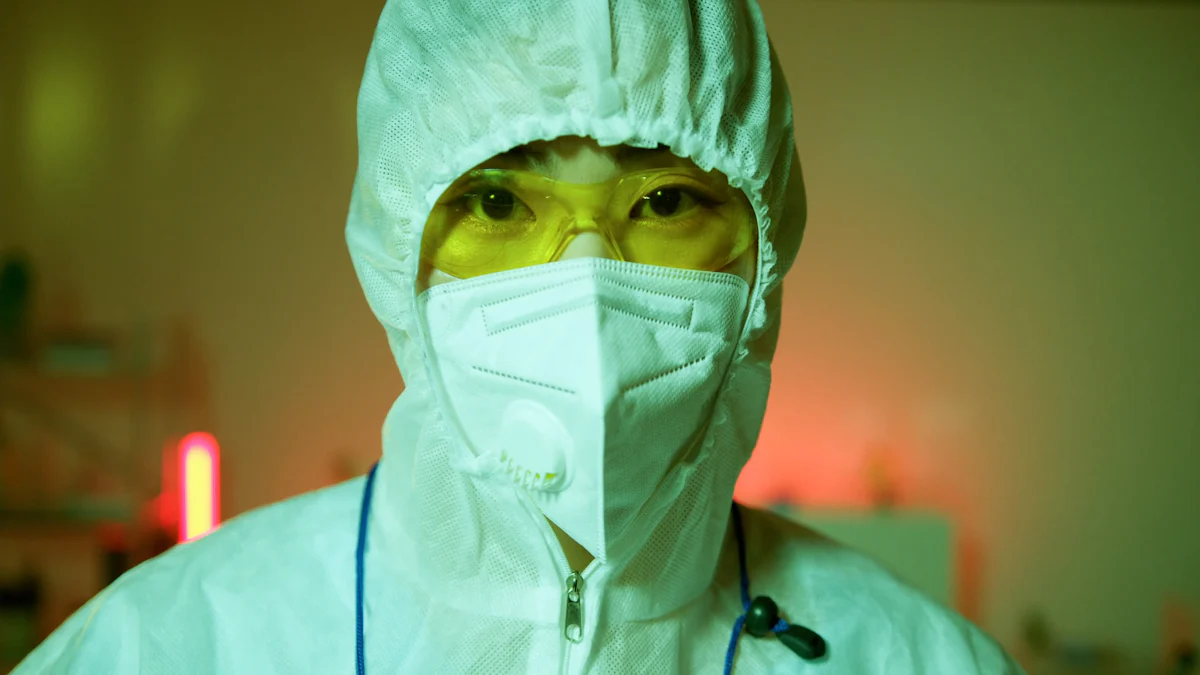
Sterility isolators play a crucial role in the pharmaceutical industry by maintaining aseptic conditions during various processes. These advanced systems create a sterile and contained environment, which is essential for conducting accurate and reliable sterility testing. By eliminating direct human intervention, sterility isolators achieve a higher sterility assurance level (SAL), significantly reducing contamination risks. They ensure compliance with stringent industry standards, such as cGMP regulations and international laws. The use of sterility isolators continues to grow, driven by the need to formulate and fill more potent products aseptically.
Applications of Sterility Isolators
Sterility isolators serve a vital role in the pharmaceutical industry, offering a controlled environment for various applications. These isolators ensure that processes remain free from contamination, thereby safeguarding product integrity and operator safety.
Drug Manufacturing
In drug manufacturing, sterility isolators are indispensable. They provide a sterile environment for aseptic processing and sterile filling. This process involves the preparation and packaging of pharmaceutical products without introducing contaminants. By using sterility isolators, manufacturers can maintain high sterility assurance levels, which is crucial for producing safe and effective medications.
Product Information:
- ST-IS Series by Tema Sinergie: Designed to meet stringent cGMP regulations, these sterility isolators offer reliable solutions for aseptic processing.
- Sterile Isolators by EREA: Equipped with gloves and cuffs, these isolators protect both processes and operators, ensuring safe handling and packaging of medicinal products.
Research and Development
Sterility isolators also play a significant role in research and development. They provide a contamination-free environment for laboratory and clinical trial applications. Researchers use these isolators to conduct experiments and tests that require aseptic conditions. This ensures that results are accurate and reliable, which is essential for developing new pharmaceutical products.
Product Information:
- EREA Isolator for Sterility Tests: Essential for carrying out sterility tests, these isolators help determine GMP compliance and marketability of pharmaceutical products. They secure processes with reliable results.
Sterility isolators, therefore, are crucial in both drug manufacturing and research and development. They ensure that pharmaceutical processes remain sterile, protecting both products and personnel from contamination risks.
Benefits of Sterility Isolators
Product Safety
Sterility isolators significantly enhance product safety in the pharmaceutical industry. They prevent contamination by creating a barrier between the product and the external environment. This barrier ensures that no contaminants enter the sterile zone during manufacturing processes. Operators also benefit from this protection, as isolators shield them from exposure to potentially hazardous substances.
Key Points:
- Contamination Prevention: Isolators maintain a sterile environment, crucial for producing safe pharmaceuticals.
- Operator Protection: They provide a safe working space, minimizing health risks for personnel.
Compliance with Standards
Sterility isolators play a vital role in ensuring compliance with regulatory standards. Pharmaceutical companies must adhere to strict guidelines, such as cGMP regulations, to guarantee product quality and safety. Isolators help meet these requirements by maintaining high sterility assurance levels.
Regulatory Adherence:
- Isolators facilitate adherence to international laws and standards, ensuring that products meet quality benchmarks.
- They support quality assurance processes by providing a controlled environment for testing and production.
Scientific Research Findings:
- State of the Art Isolators for Sterility Testing: These isolators offer the highest level of safety for both test procedures and products, ensuring reliable results even in unclassified rooms or EM GMP class D (ISO 8) rooms.
- Best Practices in Specifying and Operating Isolators: Highlight the ability of isolator technology to achieve high sterility levels in sterile manufacturing and aseptic fill/finish processes.
By integrating sterility isolators into their operations, pharmaceutical companies can ensure both product safety and regulatory compliance, ultimately enhancing the reliability and efficacy of their products.
Operational Aspects of Sterility Isolators
Types of Sterility Isolators
Sterility isolators come in two primary configurations: open systems and closed systems. Each type serves specific purposes and offers distinct advantages in pharmaceutical operations.
-
Open Systems: These isolators allow for some interaction with the external environment. They are often used when there is a need for frequent access to the isolator’s interior. Open systems provide flexibility in operations but require stringent control measures to maintain sterility.
-
Closed Systems: These isolators offer a completely sealed environment, ensuring maximum protection against contamination. Closed systems are ideal for processes that demand high sterility assurance levels. They are particularly useful in aseptic manufacturing and sterility testing, where maintaining a contamination-free environment is critical.
Both types of isolators play a crucial role in maintaining aseptic conditions, ensuring that pharmaceutical products meet the highest safety and quality standards.
Maintenance and Monitoring
Proper maintenance and monitoring are essential to ensure the effective operation of sterility isolators. These practices help maintain the integrity of the isolators and ensure consistent performance.
Cleaning Protocols
Regular cleaning is vital to prevent contamination within isolators. Pharmaceutical companies implement strict cleaning protocols to ensure that all surfaces remain sterile. These protocols often involve the use of sterilizing agents, such as hydrogen peroxide vapor, to decontaminate the isolator’s interior. By adhering to these protocols, companies can maintain a sterile environment, crucial for producing safe pharmaceutical products.
Environmental Monitoring
Monitoring the environment within and around isolators is equally important. Companies use advanced monitoring systems to track parameters such as temperature, humidity, and air quality. These systems help detect any deviations from the required conditions, allowing for prompt corrective actions. Environmental monitoring ensures that isolators operate under optimal conditions, safeguarding both products and personnel.
In conclusion, understanding the operational aspects of sterility isolators, including their types and maintenance requirements, is essential for pharmaceutical companies. By implementing effective cleaning protocols and environmental monitoring, companies can ensure that their isolators function efficiently, maintaining the highest levels of sterility and safety.
Sterility isolators play a pivotal role in ensuring pharmaceutical safety and efficacy. They provide a bacteriologically confined and airtight environment, essential for aseptic processes and sterility tests. These isolators help maintain aseptic conditions, which are crucial for compliance with Good Manufacturing Practices (GMP). As the pharmaceutical industry evolves, the importance of sterility isolators will continue to grow. Their ability to minimize contamination risks and ensure product integrity makes them indispensable tools in the development and production of safe pharmaceutical products.
See Also
Advancements in VHP Sterilization Chamber Technology
The Role of Air Showers in Cleanroom Purity
Utilizing Chemical Shower Systems in Laboratory Settings
Best Portable VHP Generators for Efficient Decontamination
Comprehending Mandatory Decontamination Shower Systems
Post time: Nov-15-2024