Comprehensive Guide to Selecting Chemical Showers
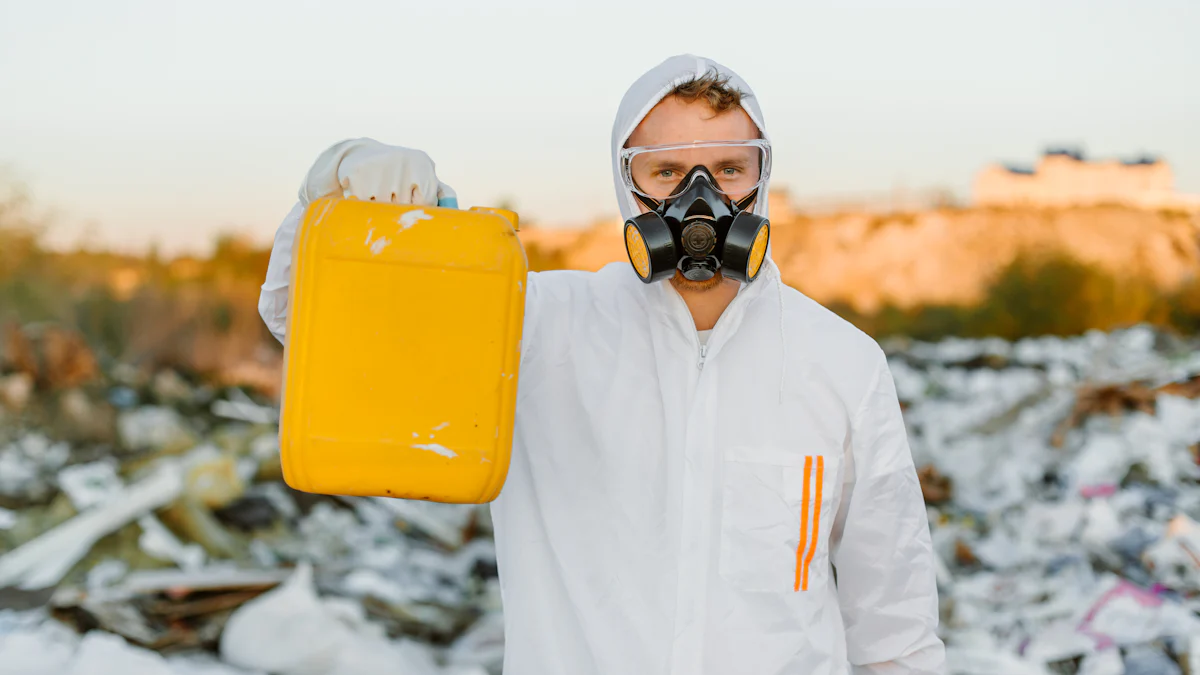
In hazardous environments, selecting the right chemical shower is crucial for ensuring safety. You must consider emergency showers and eyewash stations as essential backups. Even with excellent engineering controls, incidental exposures can still occur. These showers help minimize the effects of chemical exposure. Compliance with key standards ensures that the equipment functions effectively when needed. The ANSI Z358.1 standard, for example, provides guidelines on emergency shower performance. By adhering to these standards, you protect yourself and your colleagues from potential harm. Prioritizing safety through proper equipment selection is a vital step in maintaining a secure workplace.
Understanding Relevant Standards
Overview of ANSI Z358.1
When selecting chemical showers, you must understand the ANSI Z358.1 standard. This guideline governs the performance and maintenance of emergency showers and eyewash stations. It ensures that these facilities function effectively during emergencies. The standard covers several critical aspects:
-
Installation: Proper installation is crucial for the equipment to work correctly. The standard provides detailed instructions on how to install emergency showers and eyewash stations.
-
Water Temperature: Maintaining the right water temperature is essential. The standard specifies the recommended range to prevent further injury during use.
-
Water Flow: Adequate water flow is necessary for effective decontamination. The standard outlines the minimum flow rates required for both plumbed and portable units.
By adhering to these guidelines, you ensure that your workplace complies with safety standards. This compliance protects workers exposed to hazardous materials like formaldehyde, sulfuric acid, and sodium hydroxide.
Other Relevant Standards and Regulations
Beyond ANSI Z358.1, other standards and regulations also play a role in selecting chemical showers. These include:
-
OSHA Requirements: The Occupational Safety and Health Administration mandates suitable facilities for quick drenching or flushing of the eyes and body. This requirement ensures immediate emergency use within the work area.
-
Local and International Standards: Many governmental health and safety organizations adopt ANSI Z358.1. However, you should also consider local and international standards that may apply to your specific industry or region.
-
Testing and Maintenance Protocols: Regular testing and maintenance are vital. The standard includes directives on testing water flow, unit height, and valve functioning. Ensuring no obstructions and proper operation is crucial for safety.
Understanding these standards helps you make informed decisions when selecting emergency equipment. By doing so, you prioritize safety and compliance in your workplace.
Key Considerations for Equipment Location and Accessibility
Determining Optimal Locations
Choosing the right location for chemical showers is crucial for their effectiveness. You need to assess your workplace thoroughly to identify potential hazards. This assessment helps you determine where emergency showers are most needed. Consider areas where chemical exposure is likely, such as near storage or handling zones.
Visibility plays a significant role in location selection. Ensure that the showers are easily visible and marked with clear signage. This visibility allows quick access during emergencies. You should also consider proximity to workstations. The closer the shower, the faster the response time in case of an incident.
Additionally, evaluate the layout of your facility. Avoid placing showers in areas with obstacles or barriers. These obstructions can delay access during critical moments. By strategically placing showers, you enhance safety and ensure swift response times.
Ensuring Accessibility for All Users
Accessibility is a key factor in selecting chemical showers. You must ensure that all employees can use the equipment, regardless of physical ability. Consider the height and reach of the shower controls. They should be within easy reach for users of different heights.
The path to the shower should be clear and unobstructed. This clarity ensures that users can reach the shower quickly without hindrance. You should also consider the needs of individuals with disabilities. Install showers that comply with ADA (Americans with Disabilities Act) standards if necessary.
Regularly test the accessibility of your showers. Conduct drills to ensure that all employees know how to reach and operate the equipment. By prioritizing accessibility, you create a safer environment for everyone in your workplace.
Detailed Requirements for Water Temperature and Flow
Recommended Water Temperature
When selecting chemical showers, you must prioritize the water temperature. The ANSI Z358.1 standard specifies that the water should be between 60°F and 100°F (16°C and 38°C). This range ensures effective decontamination without causing harm to the skin or eyes. Water that is too cold can lead to hypothermia, while excessively hot water may cause burns or additional injuries.
To maintain this ideal temperature, consider installing a thermostatic mixing valve. This device helps regulate the water temperature, ensuring it remains within the recommended range. Regularly check and calibrate these valves to guarantee consistent performance. By doing so, you provide a safer environment for anyone who might need to use the emergency shower.
Ensuring Adequate Water Flow
Adequate water flow is crucial for the effectiveness of chemical showers. According to ANSI Z358.1, emergency showers must deliver a minimum flow rate of 20 gallons per minute (75.7 liters per minute) for at least 15 minutes. This flow rate ensures thorough decontamination by flushing away hazardous substances from the body.
To achieve this flow rate, ensure that your plumbing system can support the required pressure and volume. Regularly inspect the showerheads and pipes for any blockages or leaks that might impede water flow. Conduct routine tests to verify that the showers meet the necessary flow rate standards.
By maintaining the correct water temperature and flow, you enhance the effectiveness of your chemical showers. This attention to detail ensures that your workplace remains compliant with safety standards and provides optimal protection for all employees.
Comparison of Different Types of Chemical Shower Equipment
When selecting a chemical shower, you have two main options: plumbed showers and portable showers. Each type offers unique advantages and considerations, depending on your specific needs and workplace environment.
Plumbed Showers
Plumbed showers are a permanent fixture in many industrial settings. They connect directly to a building’s water supply, ensuring a continuous flow of water. This setup makes them ideal for locations where chemical exposure is frequent and predictable. You can install plumbed showers indoors or outdoors, depending on the layout of your facility. Options include wall-mounted, ceiling-mounted, or freestanding floor models.
Advantages of Plumbed Showers:
- Continuous Water Supply: Plumbed showers provide an uninterrupted water flow, crucial for effective decontamination.
- Variety of Installations: You can choose from wall-mounted, ceiling-mounted, or freestanding models to suit your space.
- Durability: These showers are built to withstand harsh industrial environments, offering long-term reliability.
However, plumbed showers require a fixed location, which may not be suitable for all work sites. You must ensure that the plumbing system can support the necessary water pressure and flow rate. Regular maintenance is essential to prevent blockages and ensure compliance with safety standards.
Portable Showers
Portable showers offer flexibility and mobility, making them an excellent choice for remote or temporary job sites. These units often come with a potable water supply, allowing you to transport them easily. For example, a Portable Safety Shower with a 528-gallon capacity can be towed behind a vehicle, providing emergency response wherever needed.
Advantages of Portable Showers:
- Flexibility: You can move portable showers to different locations as needed, adapting to changing work environments.
- Ease of Transport: Many portable units are designed for easy transportation, ensuring quick deployment in emergencies.
- Self-Contained Water Supply: These showers often include their own water supply, eliminating the need for a fixed plumbing connection.
Portable showers are particularly useful in outdoor or remote areas where plumbed options are impractical. However, you must regularly check the water supply and ensure that the unit meets the required flow rate and temperature standards.
Importance of Training and Maintenance
Ensuring the effectiveness of your chemical shower equipment requires a commitment to regular training and maintenance. These practices not only enhance safety but also ensure compliance with relevant standards.
Regular Training for Employees
Training plays a crucial role in preparing employees to respond effectively during emergencies. You should conduct regular training sessions to familiarize your team with the operation of chemical showers. This training should cover:
-
Proper Usage: Teach employees how to activate and use the chemical shower correctly. Emphasize the importance of immediate action in case of exposure.
-
Emergency Procedures: Outline the steps to take after using the shower, such as seeking medical attention and reporting the incident.
-
Location Awareness: Ensure that all employees know the locations of chemical showers within the facility. Quick access can significantly reduce the impact of chemical exposure.
Regular drills reinforce these lessons and build confidence in using the equipment. By prioritizing training, you empower your employees to act swiftly and effectively in emergencies.
Routine Maintenance and Inspections
Routine maintenance and inspections are vital for keeping chemical showers in optimal working condition. Regular checks help identify potential issues before they become critical. According to safety experts, “Regular inspections of safety showers and eyewash stations help avoid equipment failure in emergencies and keep workplaces aligned with safety requirements.”
To maintain your equipment, consider the following steps:
-
Scheduled Inspections: Conduct inspections at regular intervals to assess the condition of the showers. Check for blockages, leaks, and any signs of wear and tear.
-
Record Keeping: Maintain detailed records of all inspections and maintenance activities. These records help track maintenance needs and highlight issues that should be addressed before they lead to larger problems.
-
Testing Protocols: Implement testing protocols to verify that the showers meet the required flow rate and temperature standards. Regular testing ensures that the equipment functions correctly when needed.
By adhering to a strict maintenance schedule, you ensure that your chemical showers remain reliable and effective. This proactive approach minimizes the risk of equipment failure and enhances workplace safety.
Selecting the right chemical shower is crucial for workplace safety. You should focus on key points like understanding standards, choosing optimal locations, and ensuring accessibility. To ensure compliance and safety, follow these recommendations:
- Adhere to Standards: Ensure your equipment meets ANSI Z358.1 and other relevant regulations.
- Regular Training: Conduct frequent training sessions to familiarize employees with emergency procedures.
- Routine Maintenance: Schedule regular inspections and maintenance to keep equipment in top condition.
By prioritizing these aspects, you create a safer environment and enhance emergency preparedness.
See Also
Utilizing Chemical Shower Systems Within Laboratory Environments
Best Portable VHP Generators for Efficient Decontamination
Fogging Showers Delivered to Clients in May 2020
Advancements in VHP Sterilization Chamber Technology
VHP Pass Box: Recent Technological Innovations
Post time: Nov-14-2024